Concrete Pour Back Explained: What You Need to Know
Share this article:
Written by: Cobra Concrete Southeast
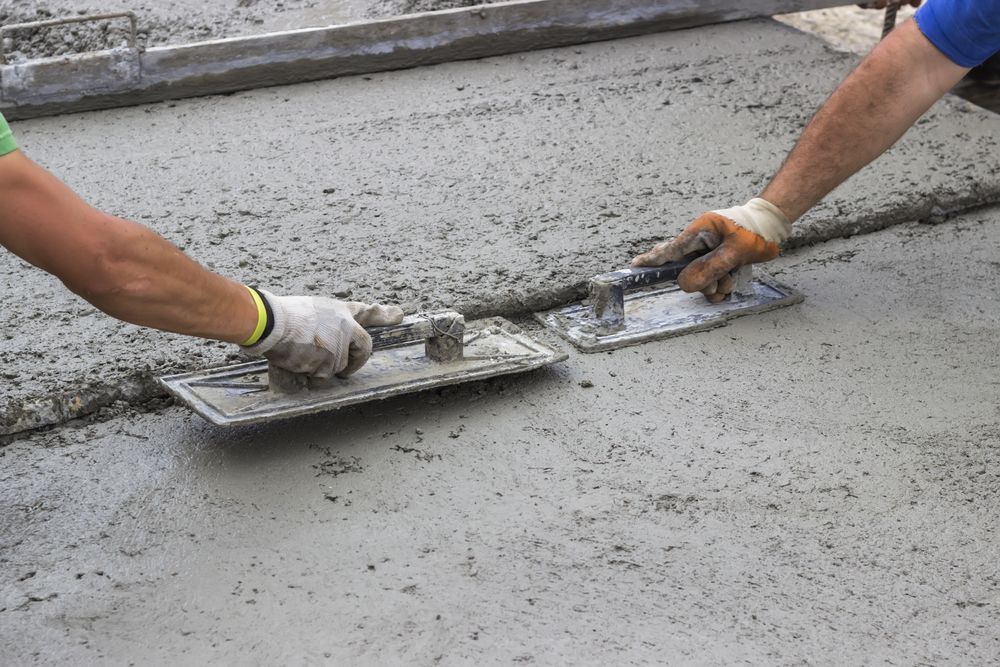
What Is Concrete Pour Back?
A concrete pour back is the process of replacing a section of concrete that was removed to perform work underneath, such as utility installation, core drilling, or foundation repair. Once the work is complete, new concrete is poured to restore the area.
Pour backs are common across commercial, industrial, and residential projects. A proper pour back is not just about filling a hole, it ensures the area is structurally sound, durable, and looks clean when finished.
Common Scenarios Requiring Pour Backs
After Plumbing or Electrical Work
When contractors install pipes or conduits under a concrete slab, they cut through the surface to access the space below. Once those systems are in place, a pour back is needed to restore the slab and prep it for flooring or traffic.
Post-Foundation Repairs
Foundation work often involves removing or cutting into a slab. Pour-backs are used to close up those access points and return the structure to full strength.
Trenching and Core Drilling
Trenching or drilling for new utilities creates openings in concrete floors and walls. After the work is done, a pour back restores integrity and smooths out the surface.
Structural Reinforcements
Upgrades to load-bearing elements often require partial slab removal. Pour backs reconnect the new and old work, helping ensure the slab performs as designed.
The Difference Between Pour Backs and Concrete Patching
A pour back is a full-depth structural replacement of concrete that was intentionally removed. It requires formwork, proper mix selection, and reinforcement to restore strength and stability.
Patching is for surface-level fixes like cracks or chips. It improves appearance but does not add structural value. If concrete was removed for access, a pour back is the proper solution, not a patch.
The Concrete Pour Back Process
A proper pour back is more than just filling a hole with concrete. It takes planning, the right materials, and careful execution to make sure the repaired section is strong, level, and long-lasting. Below is a breakdown of how the pour back process typically works from start to finish.
Step 1: Site Preparation
Cleaning and Preparing the Area
The area is cleaned, and edges are squared off. Reinforcement like
rebar or wire mesh is installed if needed to match the strength of the surrounding slab.
Ensuring Proper Reinforcement
The mix should match the existing concrete’s strength and composition. Factors like weather exposure or load requirements may call for additives that boost durability or reduce cracking.
Step 2: Selecting the Right Concrete Mix
Matching Existing Concrete Strength and Composition
The mix should match the existing concrete’s strength and composition. Factors like weather exposure or load requirements may call for additives that boost durability or reduce cracking.
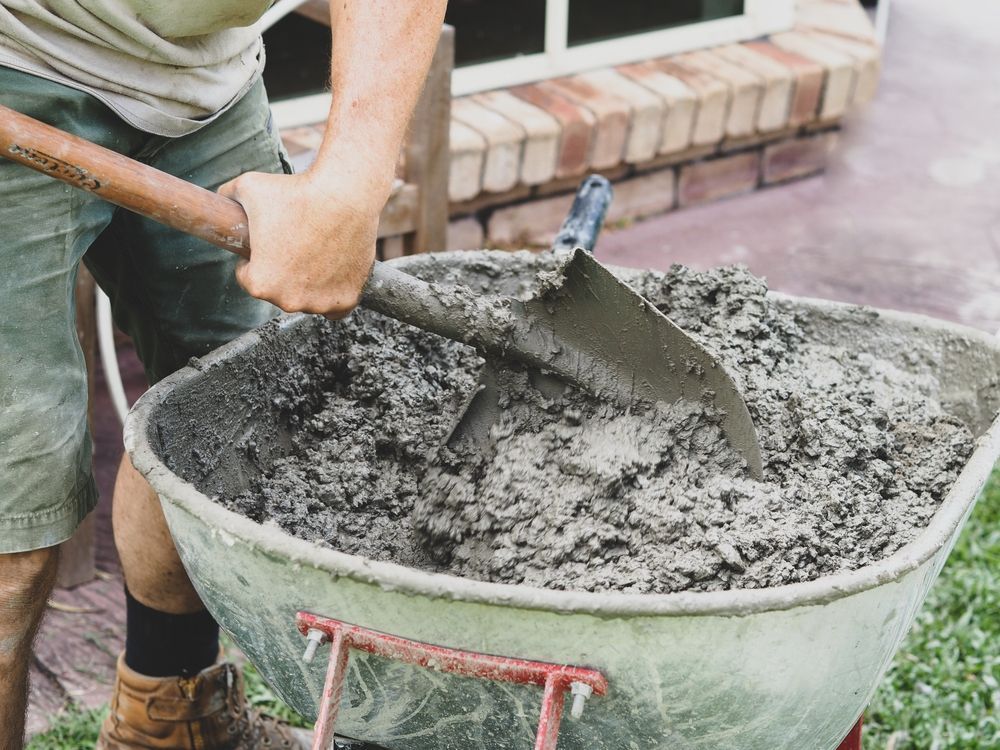
Factors Affecting Durability
Other factors, such as exposure to moisture, chemicals, or freeze-thaw cycles, may influence the choice of mix. Additives can be used to improve workability, reduce cracking, or accelerate curing times based on job site needs.
Step 3: Pouring and Leveling the Concrete
Proper Pouring Techniques & Achieving a Smooth and Even Finish
Concrete is poured evenly and worked into all corners to eliminate air pockets. The surface is finished to match the surrounding area, using tools like trowels or screeds, depending on the desired texture.
Step 4: Curing and Finishing
Importance of Proper Curing & Sealing and Finishing Options
Curing allows the concrete to gain strength. Methods include water-based curing or curing compounds. In some cases, sealing may be added to protect against moisture or wear. This is especially important in garages, warehouses, or areas exposed to the elements.
Key Considerations for a Successful Pour Back
A proper pour back is more than just filling a hole with concrete. It takes planning, the right materials, and careful execution to make sure the repaired section is strong, level, and long-lasting. Below is a breakdown of how the pour back process typically works from start to finish.
Ensuring Structural Integrity and Load-Bearing Capacity
The pour back must be able to handle the same loads as the original slab. That means matching thickness, reinforcement, and bonding strength.
Preventing Cracks and Future Damage
To avoid cracks, the mix must be designed properly, control joints should be added where necessary, and the curing process must be done right.
Meeting Building Code Requirements
Pour backs must meet local and state codes, especially on commercial and structural work. Professionals ensure the job is up to code and ready for inspection.
Cost Factors and Timeline Expectations
When planning for a concrete pour back, it’s important to understand what drives the cost and how long the process typically takes. While every project is different, a few key factors have the biggest impact on your budget and schedule.
Factors That Affect the Cost of Pour Backs
Several factors affect pour back pricing:
- Size and depth of the area
- Reinforcement needs
- Type of concrete mix
- Site access and labor requirements
- Surface finish or sealing needs
Getting an estimate from a qualified contractor is the best way to understand the total cost based on your project.
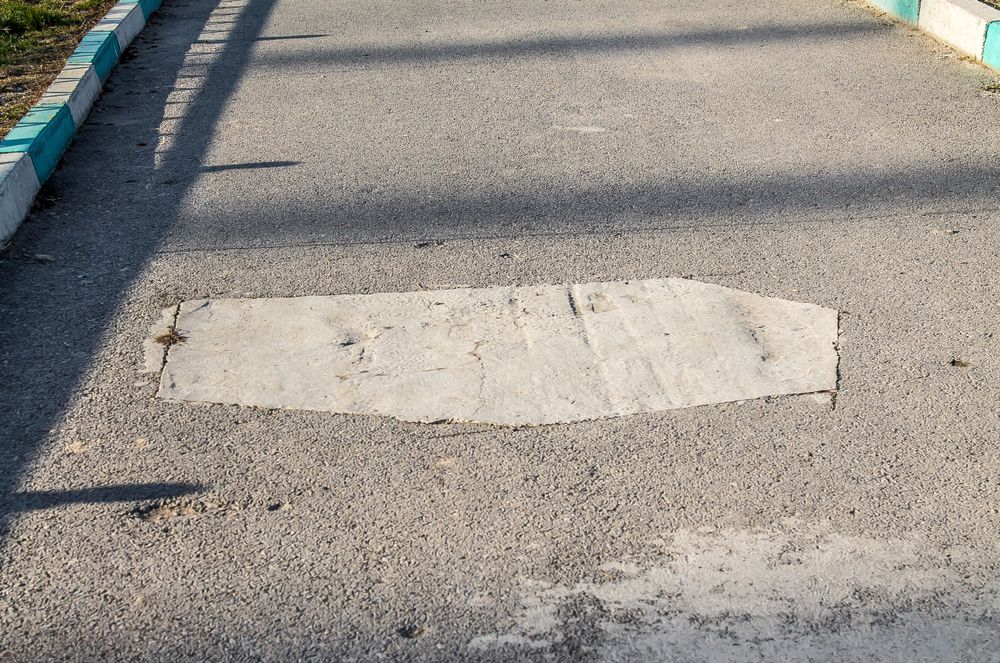
How Long Does the Process Take?
Most pour-backs take one to two days:
- Prep and forming: a few hours
- Pouring and finishing: same day
- Initial curing: 24 to 48 hours
- Full cure: 7 to 28 days, depending on mix
Fast-curing mixes are available for tighter timelines.
Fast-setting mixes are available for projects that need a quicker turnaround, but they may come at a higher cost. Always factor in curing time when scheduling the next phase of work.
Hiring Professionals vs. DIY: What’s Best for Your Project?
A proper pour back is more than just filling a hole with concrete. It takes planning, the right materials, and careful execution to make sure the repaired section is strong, level, and long-lasting. Below is a breakdown of how the pour back process typically works from start to finish.
When to Hire a Concrete Expert
If your slab supports weight, is located in a commercial space, or needs to meet inspection standards, professional help is the way to go. Pros know how to match the original concrete, handle reinforcement, and finish the job properly.
Common DIY Mistakes and Risks
DIY pour-backs often fail due to:
- Using the wrong mix
- Pouring over unclean or unreinforced areas
- Finishing too early
- Skipping curing
- Poor blending with the surrounding concrete
Mistakes like these can reduce the lifespan of the slab or even lead to failure under load. For critical applications, it's worth getting it done right.
Key Takeaways
The Importance of Proper Concrete Pour Backs
A proper pour back restores strength, stability, and appearance to a concrete slab. Cutting corners can lead to cracks, uneven surfaces, or safety issues — especially in high-traffic or load-bearing areas.
How Cobra Southeast Can Help with Your Project
Cobra Southeast specializes in concrete cutting, coring, and pour back services. Our team handles the job from prep to finish, with attention to detail and safety at every step. We work with contractors, facility managers, and property owners who need the job done right the first time.
If you're planning a project that involves concrete removal or repair, we’re here to help.
Request a quote and let us restore your slab with quality you can count on.